Coated Calcium Carbonate
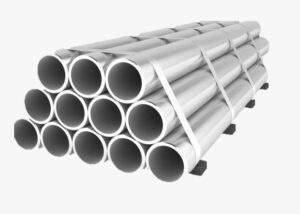
Fatty acid coated calcium carbonate (FACC) is highly compatible with polymers compared to bare calcium carbonate. Fatty acid coatings are required to improve handling in the blending process. Therefore, Shaheen provides coated calcium carbonate as a functional filler that can be used in numerous polymer industries. Improves hardness, strength and enhances surface whiteness and gloss finish. The paper industry is valued worldwide for its high gloss and light scattering properties, and is used as an inexpensive filler for making bright opaque paper. Coated calcium carbonate filler is used on the wet end of paper making machines, and allows the paper to be bright and smooth As an expander, Shaheen can represent a maximum of 30 in weight in coated calcium carbonate paint. Shaheen coated calcium carbonate is also widely used as an adhesive, and as a filler in sealants. Depending on the client’s requirement, we offer a wide range of Shaheen Coated Calcium Carbonate for the plastics and PVC industries. Maintains various properties ranging from hardness, strength, gloss and a smooth surface and low abrasion. All this has been strengthened by state-of-the-art facility labs and quality control department.
What is coated calcium carbonate, exactly, and why do we need to coat it?
Natural calcium carbonate is hydrophilic in nature and is just as invasive to organic elements as polymers. However, a cheap white filler has been forced by the plastics industry. If you mix ground calcium carbonate with plastic, the high energy of the particles creates friction. Fortunately, to reduce this resistance, we can change the surface of the particles to make them hydrophobic. Surfactants such as steiferk are common.
Calcium carbonate is used as a filler in PVC in a modified / coated surface. In this technology, a thin layer of fatty acids is coated on the surface of calcium carbonate particles. Appropriate amounts of fatty acids are used and a uniform layer of calcium carbonate is applied at controlled temperatures. Calcium carbonated treated in this way changes its chemical nature. Modification generally promotes the interaction between filler and polymeric host materials by promoting the hydrophobic and oleophilic of the original hydrophilic surface. This treated calcium carbonate can spread more well in the polymeric matrix during alloying processing.
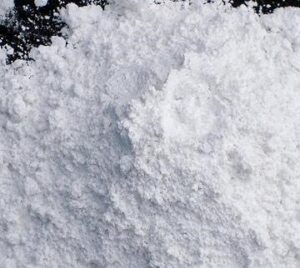
For maximum property development and forming flexibility, our surface treated carbonates are designed to give good dispersion with excellent incorporation into the copolymer matrix. Treating GCC powder with fatty acids will reduce particle interactions and allow filler dispersion in the polymer matrix. The coating can improve the dispersion of filler particles during melt mixing, reduce the absorption of other constituents on the filler surface and improve the dry flow properties of the filler. The size of the filler used can dramatically affect the impact strength of the PVC compound.
We provide different grades of coated calcium carbonate in PVC for different applications
- CC800
- CC1600
- CC2000
- CC2500
- CC5000
- CC6000
Coated calcium carbonate CCR-4 is the most important filler of plastics, rubber, coating, paper making, building materials, food, medicine, sealants and adhesives, paints etc. Its uniform particle size, even distribution makes it suitable for the functional fillers used in it. A kind of industry. This gives the polymer better hardness and increases strength (both tensile and impact strength). Coated calcium carbonate also enhances the whitening of the surface and eliminates injection.
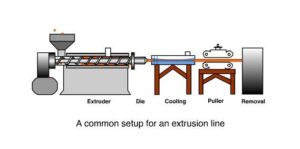
Coated calcium carbonate is used to reduce the cost of compounds in wire and cable formation while improving electrical or physical properties, it will also positively affect heat transfer and thermal conductivity.
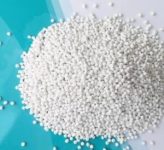
High filler loading in master batch:
Using evenly coated calcium carbonate we can achieve high filler loading. Generally, a higher filler ratio cannot be used due to the increase in surface area of ground calcium carbonate. The use of uniformly coated calcium carbonate has now solved this problem.
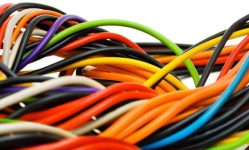
Coated calcium carbonate is used to reduce the cost of compounds in wire and cable formation while improving electrical or physical properties, it will also positively affect heat transfer and thermal conductivity.